Walk in my boots: Eliza O'Day
When it comes to getting raw materials into Australia by sea, Eliza O'Day is right at the helm. From ports to paperwork, she manages the complex and often unpredictable process of importing the dry bulk materials Boral needs to keep moving.
Boral proudly produces raw materials here in Australia, including clinker from our Berrima kiln using limestone from Marulan. But to meet national demand, we also import around 1.2 million tonnes of materials each year, including clinker, slag and gypsum. That’s where Eliza’s expertise comes in.
Ports, plans and paper trails
Eliza manages these shipments into two key ports. There’s our new, purpose-built Cement plant at the Port of Geelong, and Fisherman’s Island at the Port of Brisbane, which supports our Sunstate Cement joint venture with Adbri in Queensland.
Our Geelong facility ensures a steady supply to southern states. And our deliveries into Brisbane keeps Sunstate stocked and ready to go.
Before anything sails, Eliza works closely with our Sales and Operations teams to forecast demand. It’s a juggling act, looking back at previous volumes, adjusting to what’s happening on the ground and looking forward too.
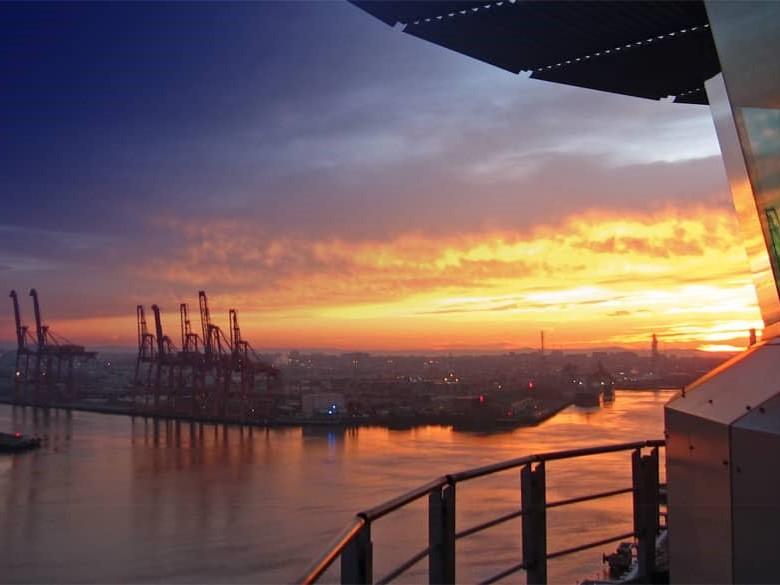
37 vessels, tonnes of detail
Each year, Boral charters about 37 vessels, each carrying between 25,000 and 49,000 tonnes of materials. Every shipment has its own charter party agreement, usually handled with help from partners like Pacific Basin and brokers like Midship.
Once the supplier confirms the cargo is ready, Eliza books the vessel, oversees loading and tracks the shipment across the sea. Most trips take 20 to 23 days to reach Australia.
At port, the cargo is unloaded by stevedores using the ship’s cranes. In Geelong, materials feed straight into Boral’s plant via conveyor. In Brisbane, they go directly into Sunstate’s storage and handling systems.
In shipping everything is big, including the costs for delays. A single day’s delay could cost up to USD $16,000 to cover the ships’ waiting time. At the current exchange rate, that could amount to nearly AUD $25,000 a day.
Getting the planning right and coordinating the timely discharge of the cargo is a vital part of her role.
Keeping stock afloat
Timing is everything. Eliza monitors stock levels and works within minimum and maximum thresholds to keep sites running. If a shipment needs to be delayed, she can usually make it happen. Speeding one up, though? That’s a tough ask.
“It’s a legally complex and surprisingly old-school process,” Eliza says. “We still use original paper documents to release every shipment. If an important document goes astray, the whole vessel can be held up.”
Freight with responsibility
Eliza’s role goes well beyond logistics. Boral holds its international supply chain to high standards, from modern slavery compliance and vessel safety to environmental impacts and ethical performance.
She tracks the performance of every link in the chain, including suppliers, charter companies, stevedores and brokers, while also keeping a close eye on global factors like fuel prices, trade tensions and political unrest.
With cool-headed precision and a sea of knowledge, Eliza O'Day helps keep Boral’s supply chain strong, steady and sustainable.
Now that’s a freight job well done.
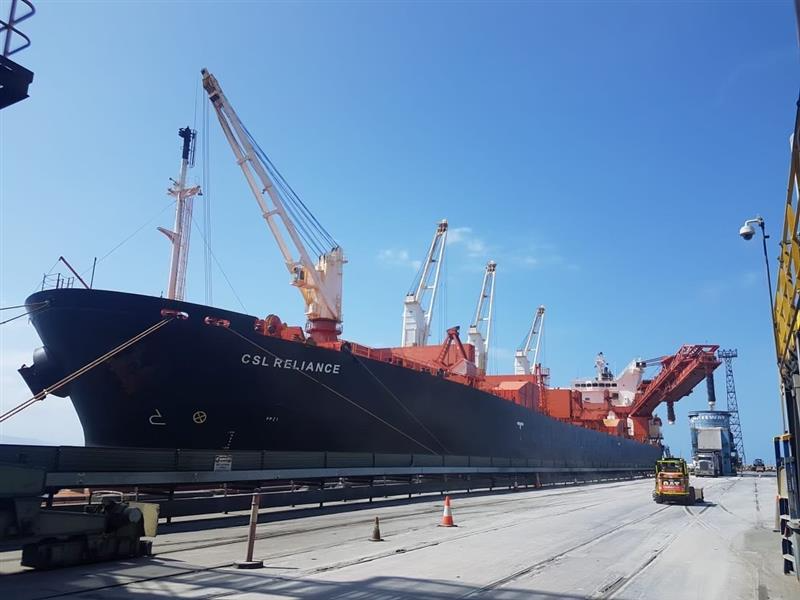
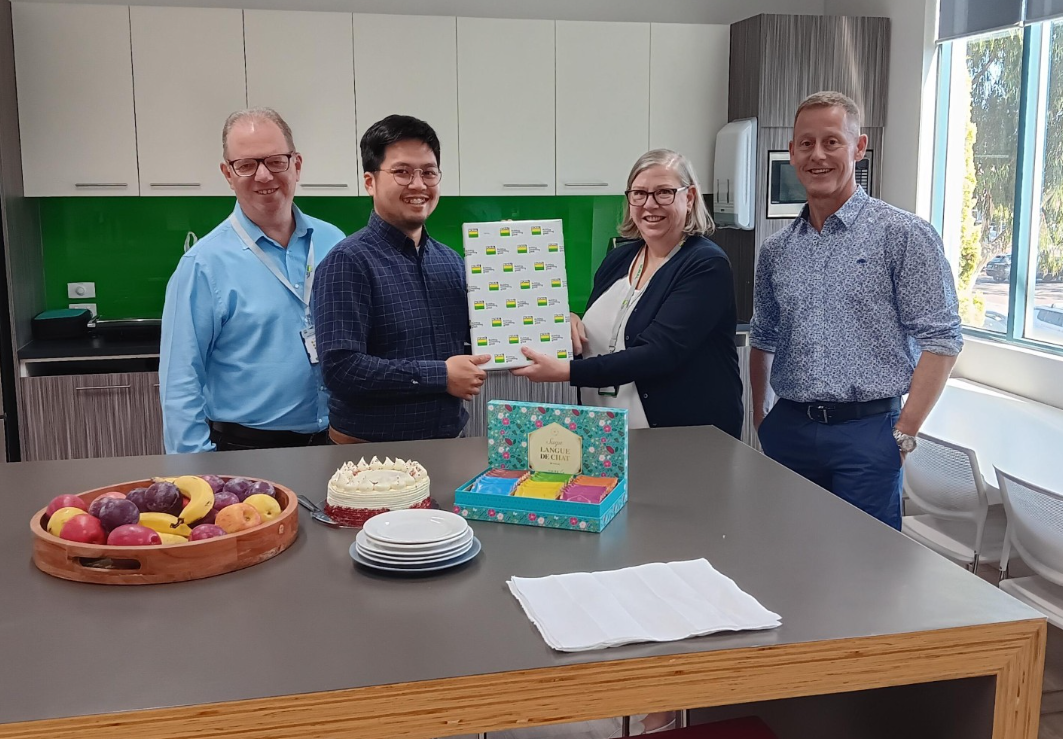
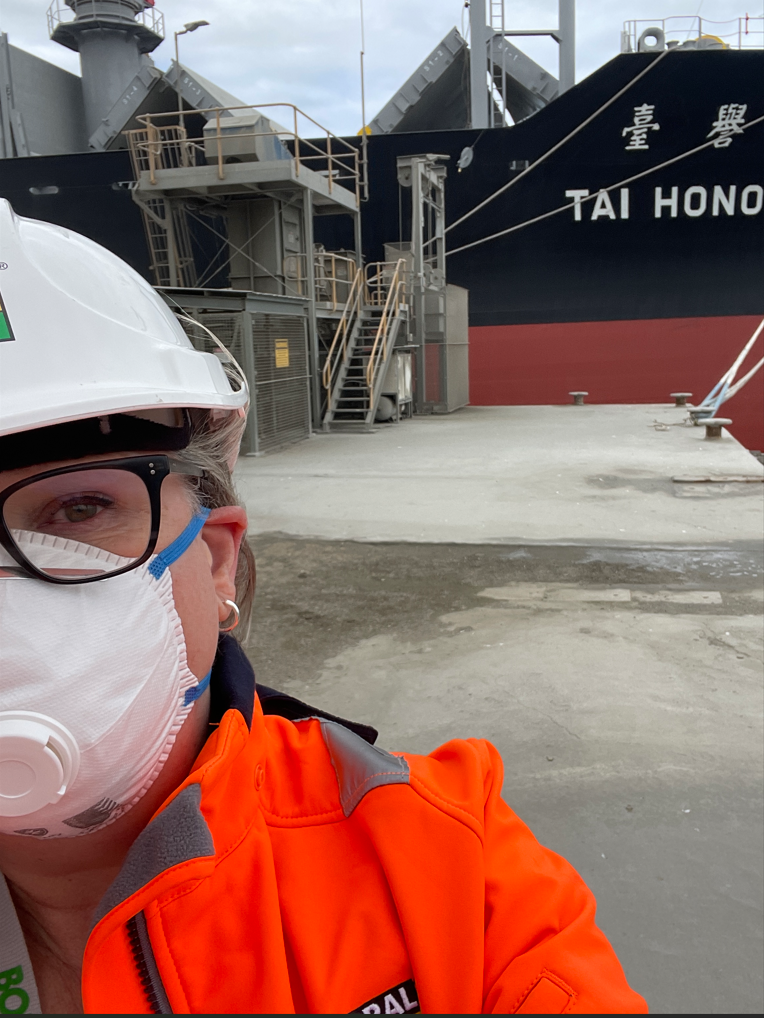
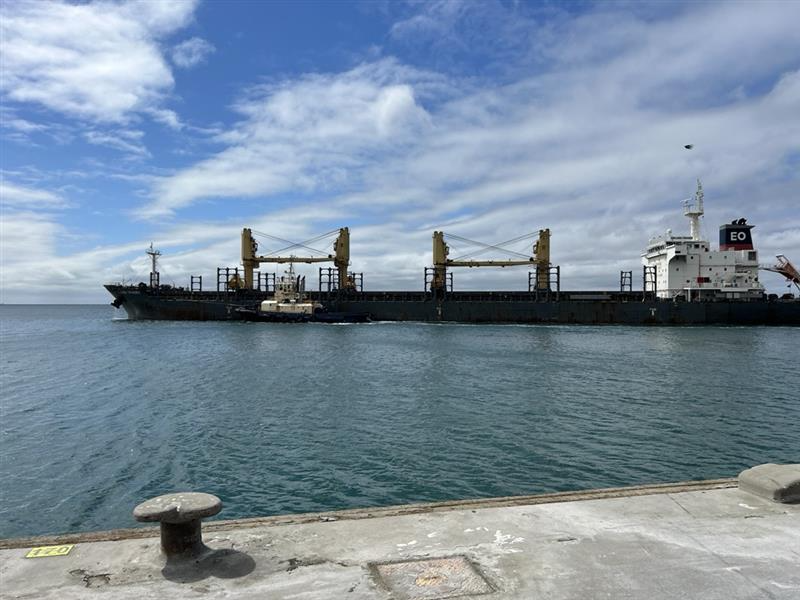